The Jellyfish Robot
︎Digital/Physical Fabrication
︎Soft Robotics
︎Electronics
︎Biodesign, Biomimicry
Collaborators:
Aimilios Davlantis-Lo, Young Ju
This small aquatic robot mimics the swimming movements of the jellyfish, which uses its body to propel itself and push the water away.
This design uses 1) soft robotics principles and 2) kirigami, a type of 3D origami, to faciliate kinetic motions through the virtue of its geometry rather than highly engineered joint designs.
Soft robotics encourages the integration of physically flexible bodies with electronics to allow navigation not conducive to rigid-body robotics.
Nature is a frequent source of inspiration for soft robotics, and this project uses the beautiful efficiency of the jellyfish’s movements to navigate an aquatic environment.
This design uses 1) soft robotics principles and 2) kirigami, a type of 3D origami, to faciliate kinetic motions through the virtue of its geometry rather than highly engineered joint designs.
Soft robotics encourages the integration of physically flexible bodies with electronics to allow navigation not conducive to rigid-body robotics.
Nature is a frequent source of inspiration for soft robotics, and this project uses the beautiful efficiency of the jellyfish’s movements to navigate an aquatic environment.
The Robot’s Movements:
(Please allow 5 seconds for video loading)

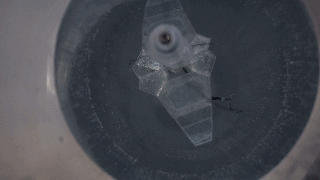

Geometric experiments: Inspired by the Japanese tradition of Kirigami, a type of 3D origami where the paper is cut as well as being folded, this jellyfish robot design facilitates kinetic motions through the virtue of its geometry rather than highly engineered joints.

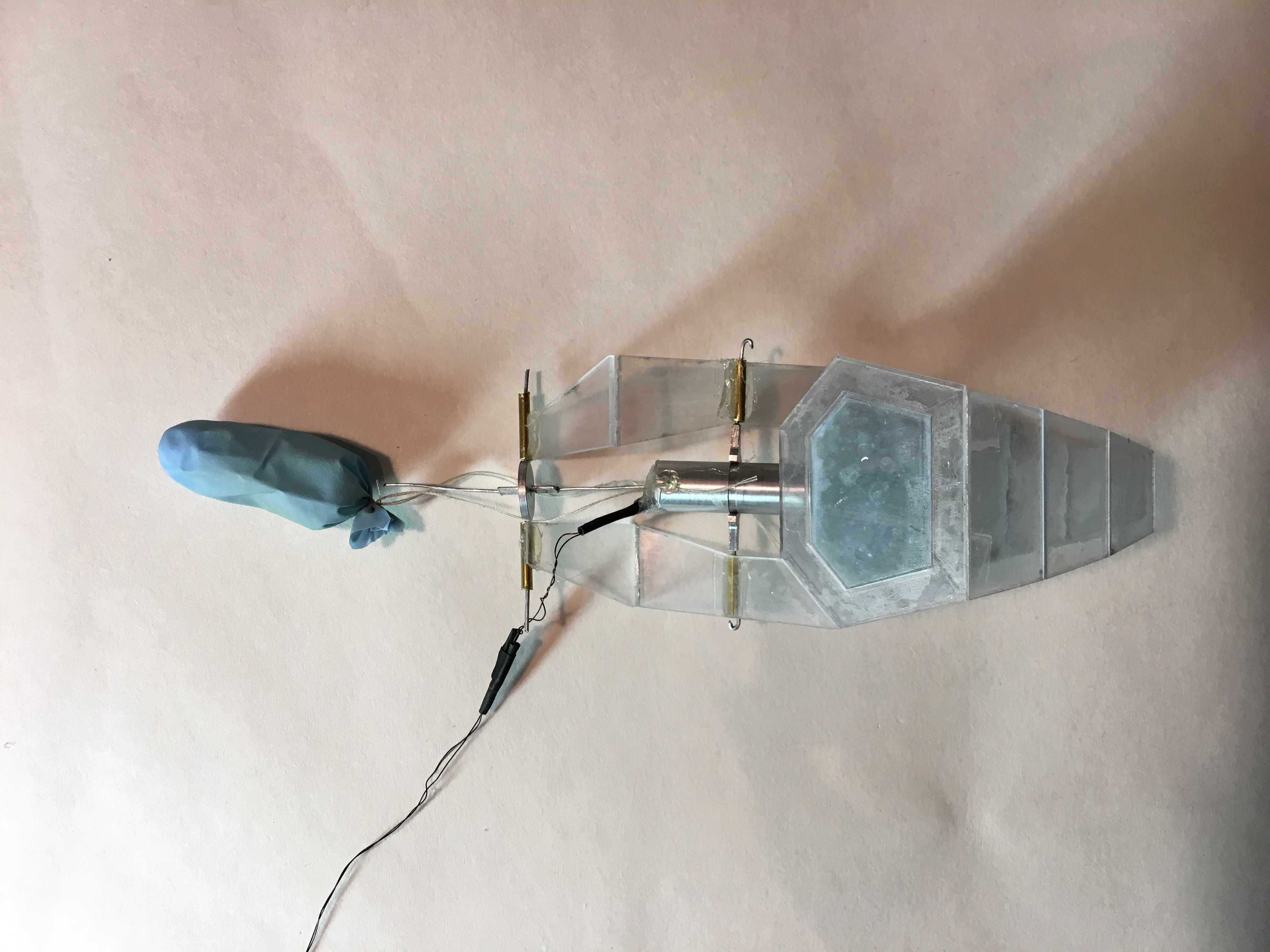
Custom-made linear solenoid parts: fabricated by machining metal, with design considerations for heat sink and elongated distance of movement.

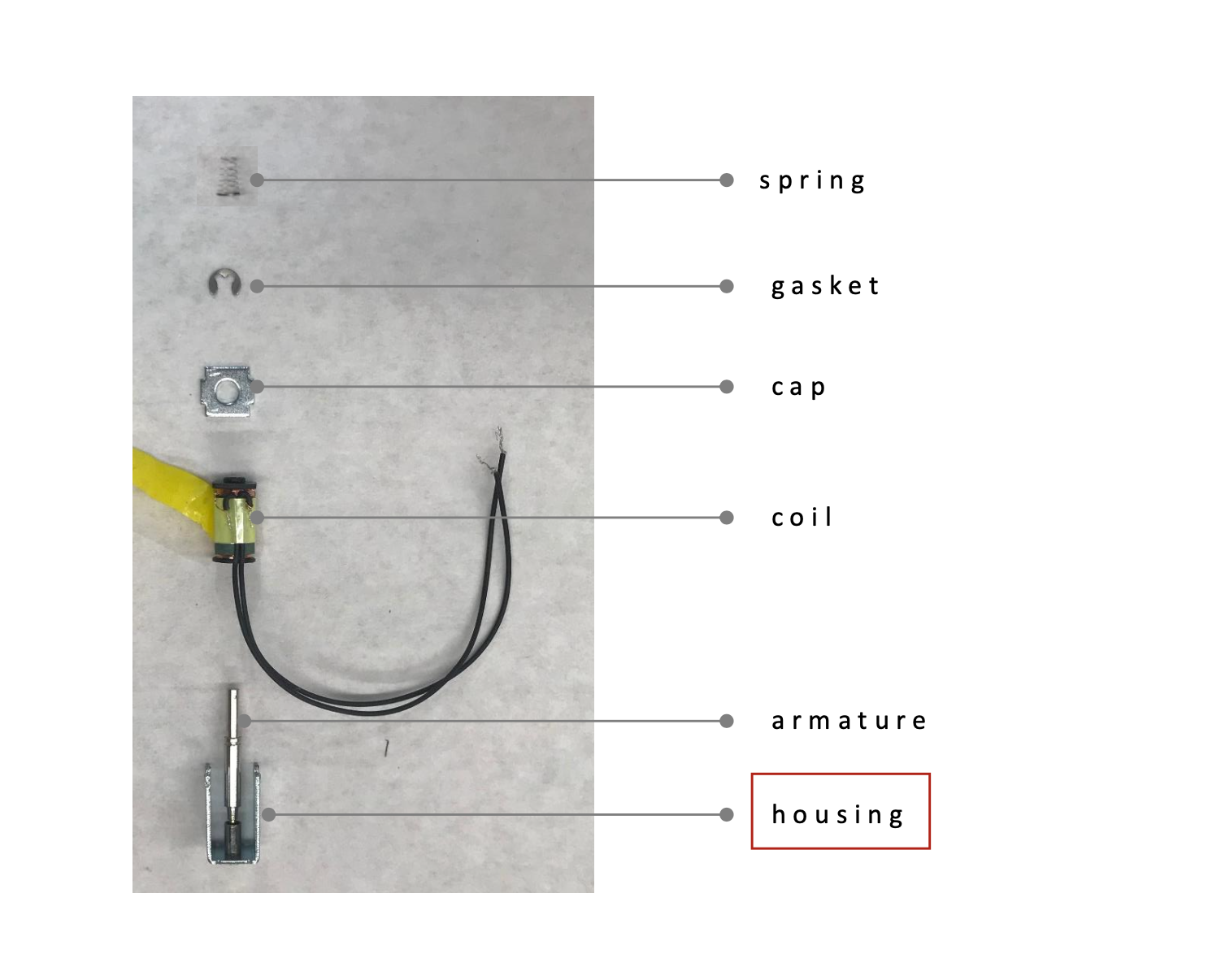


Electronics schematic: the primary component is a solenoid actuator, which moves in a linear motion when magnetized by an electric current.
![]()
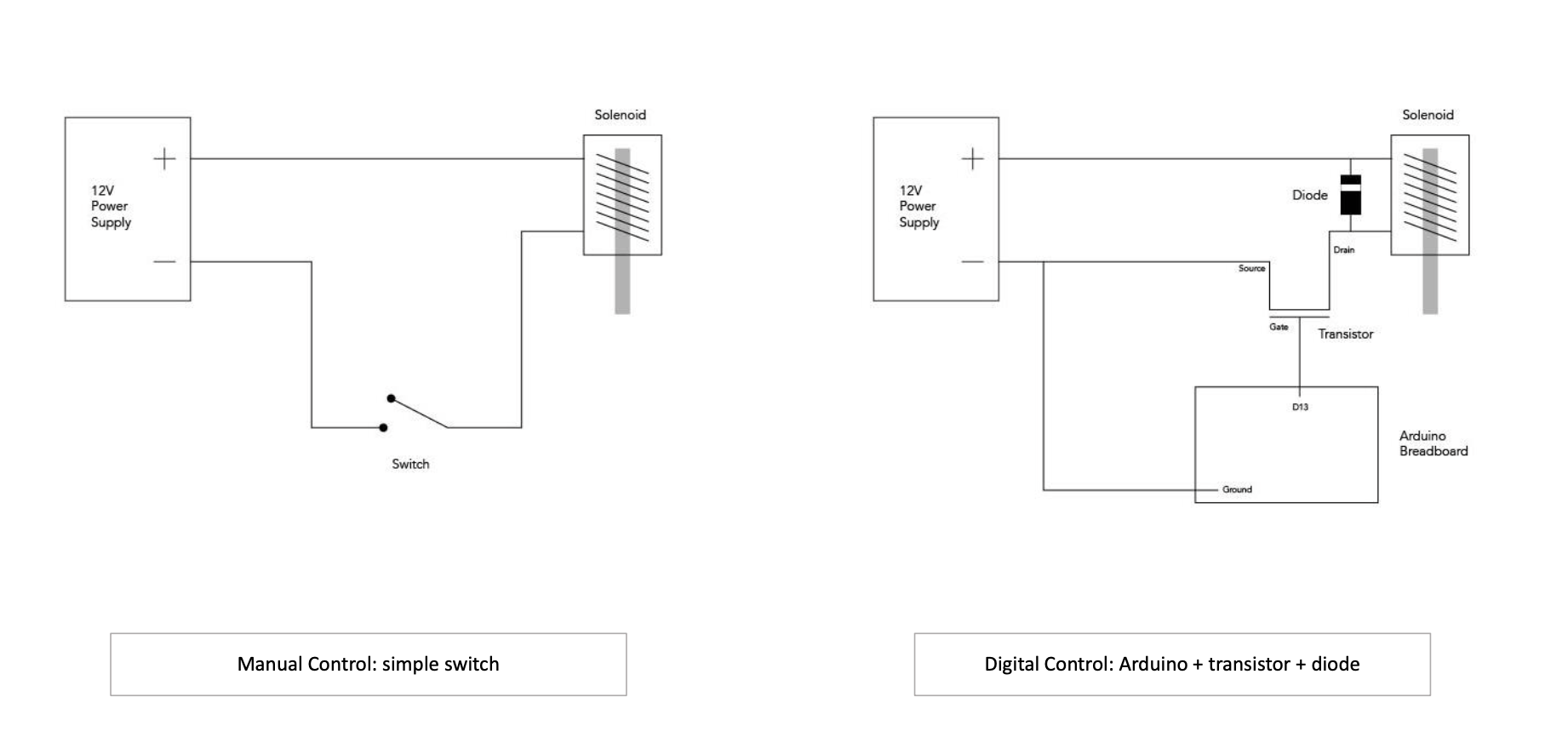
Prototyped variations for Lasercut PETG plastic: rapid iterations to test a variety of design possibilities - an enlarged scoop, cutouts to minimize drag, adding scorelines to create floppiness, and a combination of these design elements.
Iterations: prototypes through various engineering and kirigami tests
![]()




Iterations: prototypes through various engineering and kirigami tests
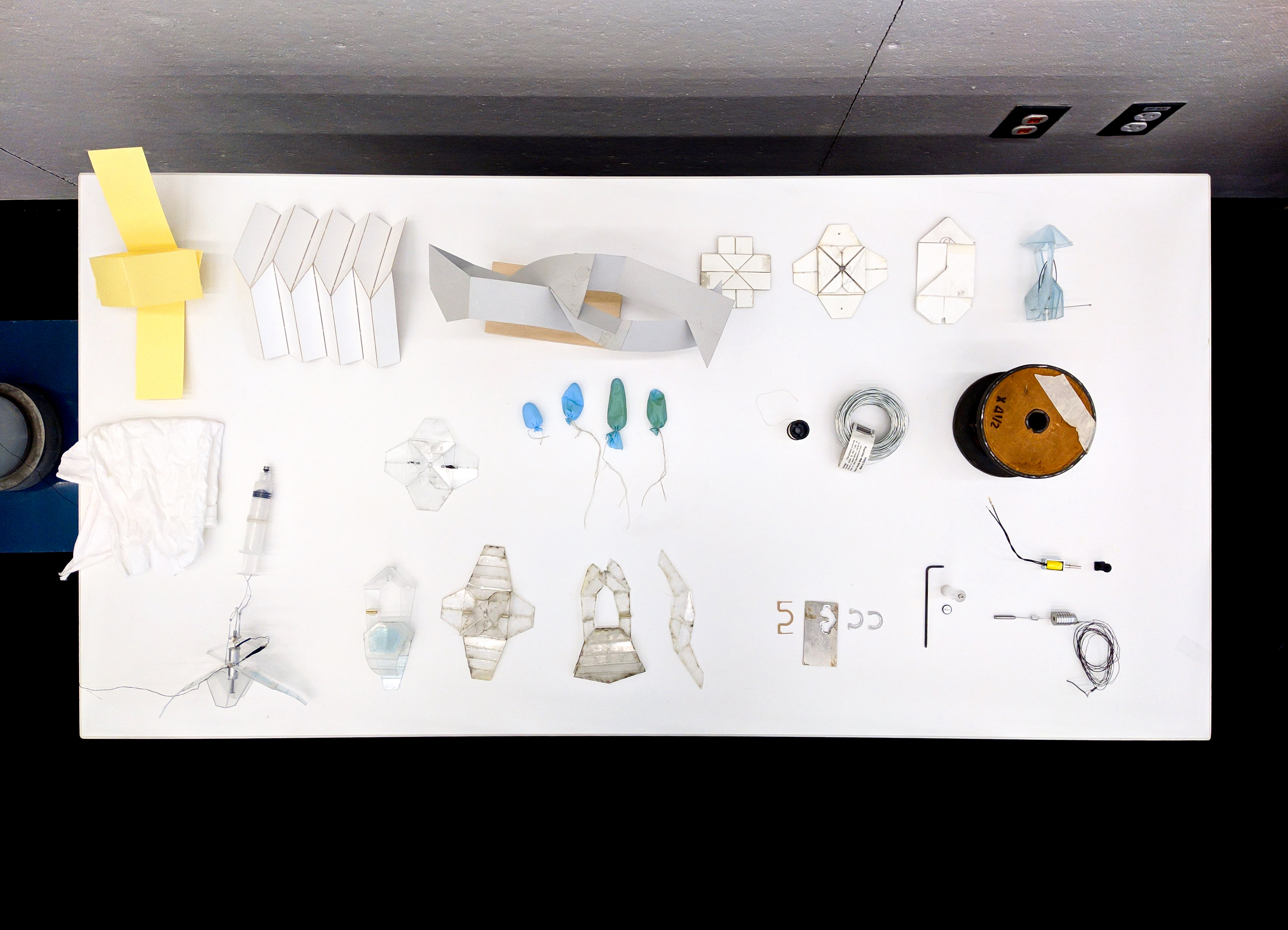
Collaborators: Aimilios Davlantis-Lo, Young Ju
Advisor: Chuck Hoberman
Materials: 1/32” PETG sheets, bristol paper, metal, solenoid linear actuator parts, wire, syringe, balloon
Fabrication Techniques: Metal precision-machining (to create a custom heat-sink body for the linear solenoid actuator), lasercut PETG plastic sheets, Arduino electronics and programming.
Advisor: Chuck Hoberman
Materials: 1/32” PETG sheets, bristol paper, metal, solenoid linear actuator parts, wire, syringe, balloon
Fabrication Techniques: Metal precision-machining (to create a custom heat-sink body for the linear solenoid actuator), lasercut PETG plastic sheets, Arduino electronics and programming.